Industries all over the world are taking up sustainable methods to decrease their environmental influence because of increasing worries about the planet. The plywood manufacturing field is also changing, with many companies now using eco-friendly approaches to make good quality plywood while focusing on saving our environment from harm. This blog post looks at current trends and new developments in sustainable plywood production, and how these methods are influencing the future direction of this industry.
Responsibly Sourced Timber
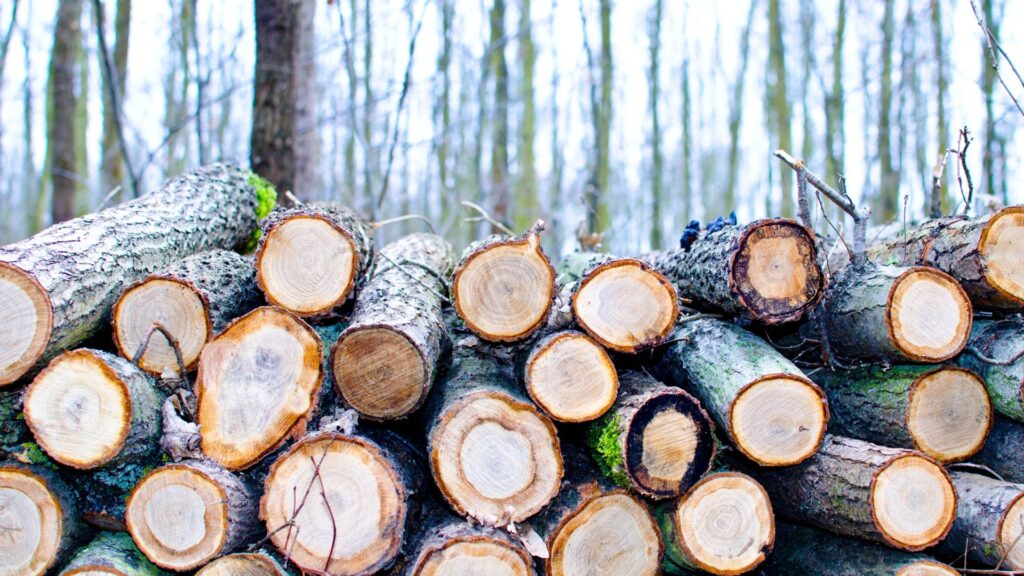
Another important advance in eco-friendly plywood making is the shift towards using timber that comes from responsible sources. Today, a lot of manufacturers give importance to getting wood from forests which are managed sustainably. Collaborations with groups like Forest Stewardship Council (FSC) and Programme for Endorsement of Forest Certification (PEFC) guarantee that raw materials come from forests following stringent environmental and societal regulations.
Using lesser-known timber species is part of responsible sourcing for plywood. This keeps balance in wood selection, decreasing stress on popular woods that may be overused. The variety assists in maintaining forests’ sustainability and conserving biodiversity.
Resource Efficiency
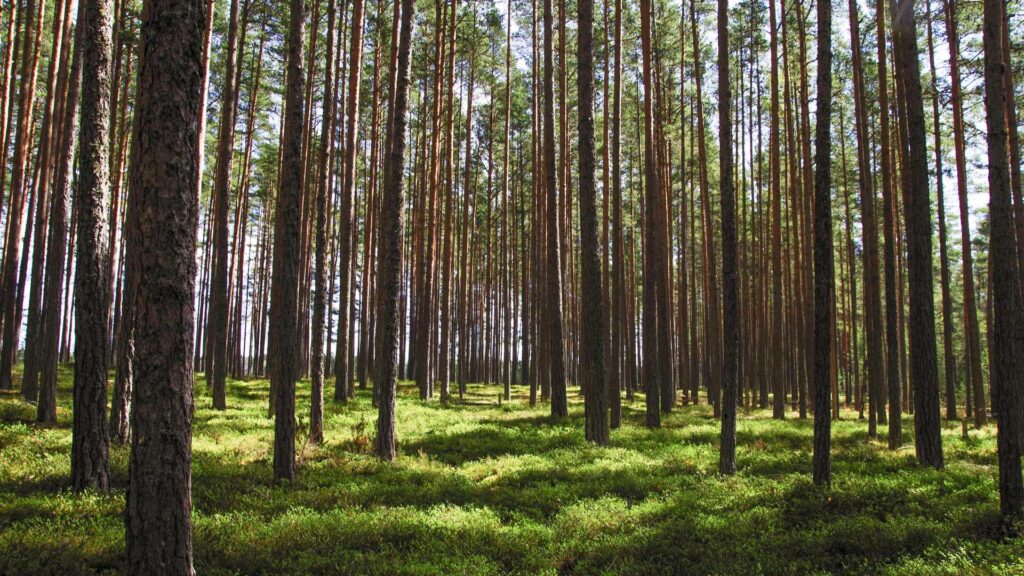
Today’s plywood factories make use of cutting-edge technology to ensure their production process is highly efficient, wasting less and producing more. By using computer-controlled cutting systems, manufacturers can cut wood veneers with great precision which helps reduce the amount of material that becomes scrap. This technology also brings new opportunities for making complex designs and patterns, leading to more appealing and sustainable plywood products.
Furthermore, numerous businesses are using closed-loop water systems that recycle and reuse water in the manufacturing procedure. This method of treating and recirculating water assists plywood makers to decrease their use of fresh water considerably, thus aiding in the preservation of this valuable resource. A few factories have accomplished zero liquid discharge, making certain that no wastewater gets released into the environment.
Eco-Friendly Adhesives
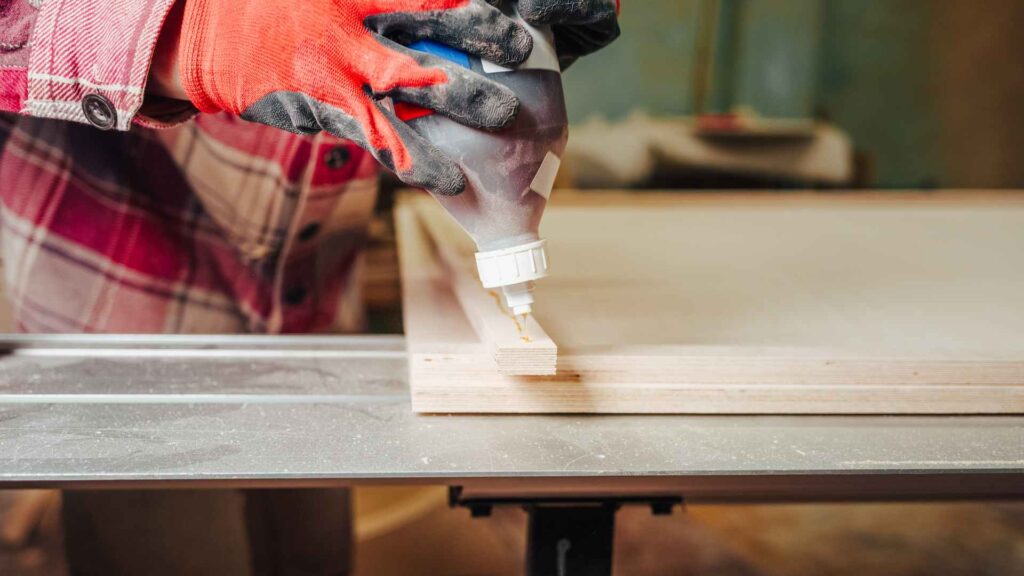
Eco-friendly adhesives are another big change in the plywood industry. In the past, making plywood used resins with formaldehyde that release bad volatile organic compounds (VOCs). This puts both workers and consumers at risk of health problems. But now, new adhesive technology has given rise to low-emission choices without formaldehyde.
Eco-friendly adhesives like soy-based resins and polyurethane help lessen the effect on the environment from making plywood while also improving indoor air quality. Soy-based adhesives, which are obtained from renewable resources, provide a more planet-friendly choice than resins made from petroleum. They possess superb bonding characteristics and guarantee that the final products of plywood are robust and long-lasting.
Energy Efficiency
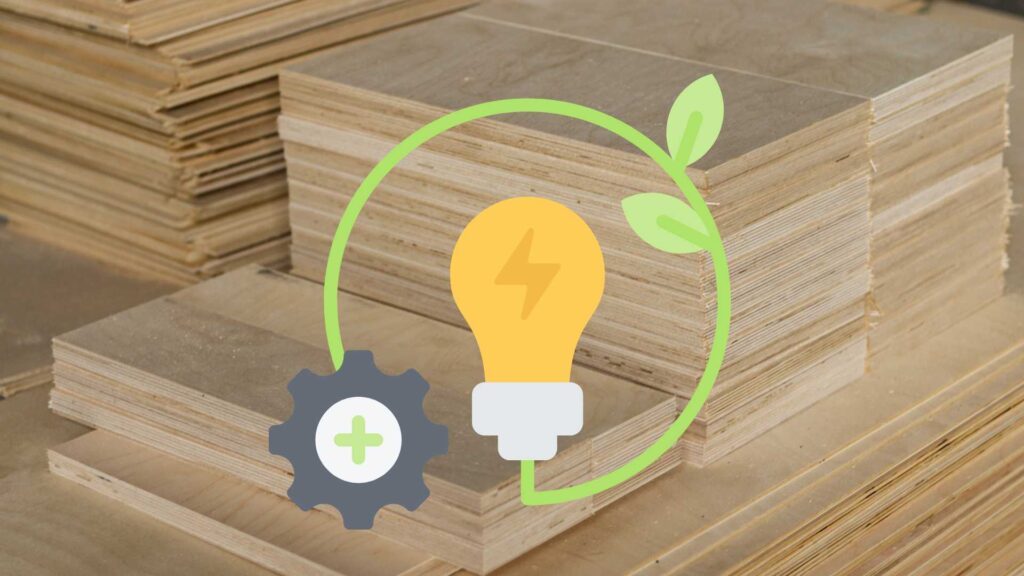
The use of energy in an efficient way is a main concern for sustainable plywood makers. Many companies have put money into renewable power sources, like solar panels or biomass boilers to energize their factories with such clean energy. This move helps plywood manufacturers cut down on the amount of carbon they produce and actively participate in fighting against global warming.
On the tops of factories, solar power systems have the ability to produce a large part of the energy needed for making plywood. Boilers that use biomass, by burning wood waste and other natural materials, are an alternative source for making renewable energy instead of fossil fuels. Some companies who make plywood have managed to make enough energy on their own using different types of renewable technology together.
Also read: Elevating Eco-friendly Living with Chic Interior Design
Waste Upcycling
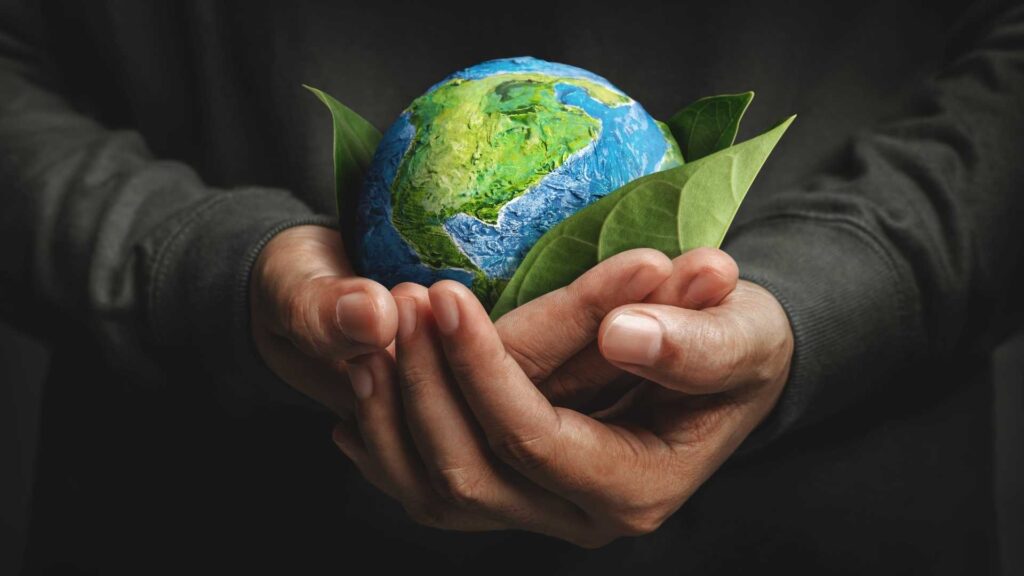
The plywood manufacturing industry is looking into new ways to recycle and reuse waste materials. For example, wood chips, sawdust and leftover items from making plywood could be turned into useful things like biomass fuel, mulch or environment-friendly packaging materials.
An instance is sawdust that gets squeezed into wood pellets. These are used as a renewable and efficient fuel for heating systems. Wood chips can also be utilized in landscaping tasks, like keeping soil moist or stopping weed growth. To give an example, some businesses make biodegradable packing materials from waste wood to promote environment-friendly packaging instead of using plastic.
Growing Demand for Sustainable Plywood
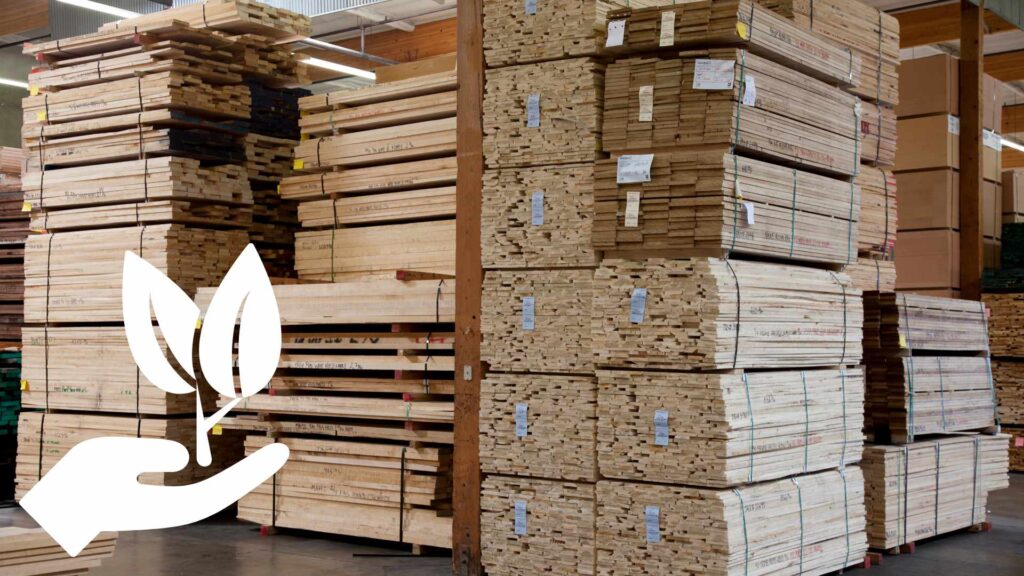
With growing consciousness among consumers about sustainable products, eco-friendly plywood is getting popular in different uses. People like architects, designers and customers are searching for plywood made with methods that support sustainability in areas such as green building projects and furniture manufacturing.
For aiding customers in recognizing plywood items made sustainably, certification plans and eco-labels have been created. For instance, the FSC and PEFC labels show that wood used in the plywood is from forests managed with responsibility. Different labels like California Air Resources Board (CARB) certification ensure that the plywood meets rigorous emission standards set for formaldehyde and other VOCs.
Also Read: Sustainable Wood: Benefits for the Construction & Design Industry
Wrapping up
The business of plywood manufacturing is going through a green revolution, where eco-friendly methods are becoming common. Starting with the use of wood from responsible sources and adhesives that meet environmental standards, to making production processes energy-saving and reusing waste materials – plywood makers are showing their dedication towards safeguarding nature. The world of plywood is stepping towards sustainability, not just to help the environment but also to secure its own future.